Selecting the correct fastener length
High quality fasteners provide consistent and reliable performance in concrete, block, masonry, and steel applications. Choosing the correct fastener for the job will assure professional results.
A. Determine thickness of material being attached.
B. Fastener must be long enough to drive approximately 1" into concrete, cement block or penetrate thickness of steel.
Power level guide for loads
All loads are color coded and load level numbered. As the number increases, the power level increases.
Always start with the lightest load. If the fastener does not set completely, use the next higher load and repeat the process.
Fastening to concrete
As the fastener enters the concrete, extreme pressures and heat are created. This creates a bond that provides high loading strength in concrete snugly and provides tool protection.
Fastening to steel
The resilience of steel provides a clamping effect to the fastener. This combined with the tremendous heat that is created, provides a welding and clamping effect to give maximum holding power
Fastening placement and penetration
The following represents the minimum edge and spacing requirements, plus base material thickness requirements:
Concrete
- Edge distance. Do not fasten closer than 3 inches from the edge of concrete. If the concrete cracks, the fastener may not hold and may allow the fastener to ricochet, causing serious injury or death to the operator or bystanders.
- Recommended minimum fastener spacing. Setting fasteners too close together can cause the concrete to crack. The recommended MINIMUM DISTANCE between fastening is three (3) inches. Never attempt a fastener application too close to another previously inserted fastener to prevent the second fastener from ricocheting off the previously installed fastener. A ricochet can result in serious injury or death to the operator or bystanders.
- Concrete thickness. It is important that the concrete be at least three (3) times as thick as the fastener penetration. If the concrete is too thin, the compressive forces forming at the fastener’s point can cause the free face of the concrete to break away. This creates a dangerous condition from flying concrete and/or the fastener and also results in a reduction of fastener holding power.
Steel
- Edge distance.The recommended edge distance for a fastener to the edge of steel is 1/2 inch. Never fire the tool within 1/2 inch of the edge of a steel base material because the steel may bend or break off, allowing the fastener to ricochet, causing serious injury or death to the operator or bystanders.
- Recommended minimum fastener spacing.The recommended minimum distance between fastening is 1 inch. Never attempt a fastening application too close to another previously inserted fastener to prevent the second fastener from ricocheting off the previously installed fastener. A ricochet can result in serious injury or death to the operator or bystanders.
- Steel thickness.Do not fasten into steel base material thinner than the fastener shank diameter. Holding power will be reduced and the fastener may be over-driven, creating a dangerous situation to the operator or bystanders due to a free-flying fastener.
How to select a powder actuated fastener
Drive pins are used to directly fasten an object (permanent installation).
Threaded studs are used where the object fastened is to be removed or where shimming is required. The following shows how to determine shank and thread length. Required penetration is determined by load requirement (illustrated in the following examples).
Ramset fasteners may be specified by their type or catalog number to satisfy fastening requirements.
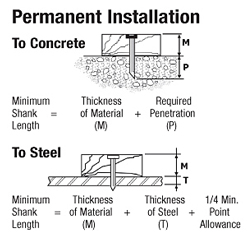